Products Used | ApronSeal™ Single Skirting , External Wear Liner |
---|---|
Product Types Used | Transfer Point Solutions , Belt Sealing |
Solution | Installation |
Industry | Coal-Fired Power |
Customer | NIPSCO Michigan City Generating Plant |
Problem
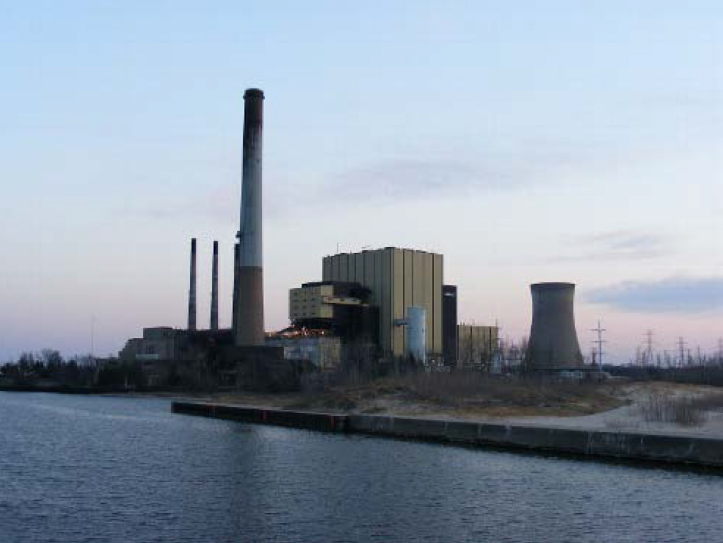
At the Northern Indiana Public Service Company (NIPSCO) Michigan City Generating Plant, 5000 tons per day of PRB coal are metered via belt feeder onto conveyors and into the plant's ten bunkers. With surge of material as railcars unload, combined with the high head pressure from the hoppers, the belt feeders suffered extensive spillage. This spillage was compounded by the worn-out condition of the chutes. In early 2009, a conveyor fire—fortunately without serious damage, injury or system outage—emphasized the problem and sent Michigan City plant personnel in search of a solution.
Solution
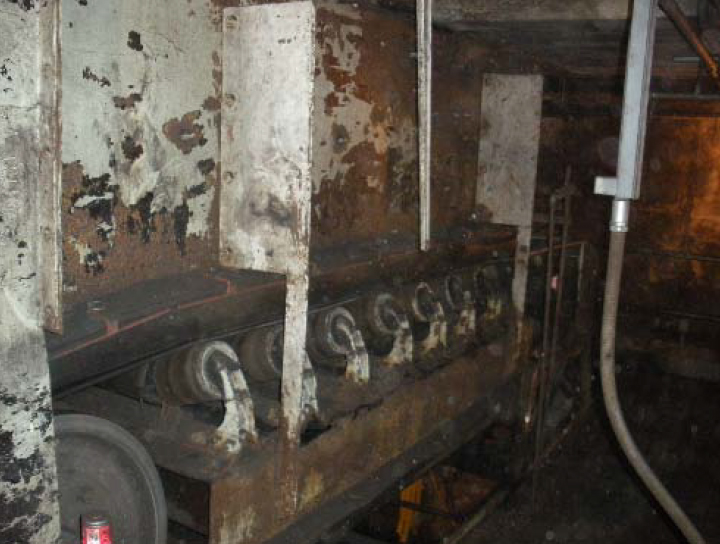
To upgrade its system and reduce spillage, NIPSCO Michigan City elected to install EVO® External Wear Liner from Martin Engineering on the four feeders below the rail car dump, as well as on the two feeders from the reclaim system. Applied on the outside of the chute, the retrofit wear liner is easy to install without requiring confined space entry. And it can be installed without extensive tear-out of the existing chutes. Rather than waiting for a full plant outage, the installation at NIPSCO Michigan City was completed during a single-shift downtime by technicians from MartinPLUS® Services.
Results
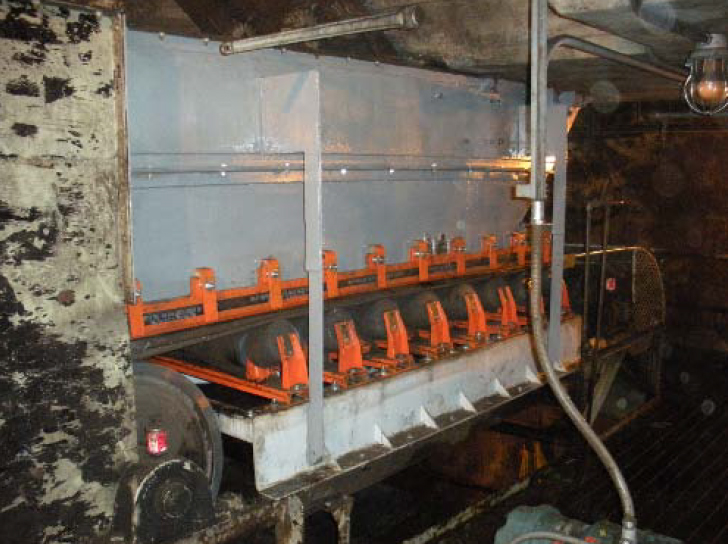
Plant management at NIPSCO Michigan City saw immediate results following the installation of the EVO® External Wear Liner. "We are pleased with both the work of the Martin Engineering installation crews and the performance of the Wear Liner," said Terry Weiler, Maintenance Supervisor. "Because it went on easily, we could complete the upgrade without an extensive outage. It refurbished our system and helped us reduce the fugitive material. We are now looking at using the EVO® External Wear Liner to upgrade other conveyors in the plant."
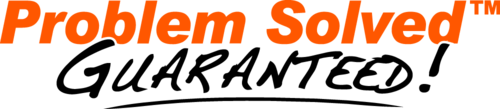
We've solved your problem somewhere before!
While your problem seems unique and frustrating, with 70+ years of solving similar problems around the world, and with the most experienced and educated people on our teams, we can assure you that we’ve “Been There, Done That.” At least close enough to know what needs to be done next and adjust for your situation.
Put Us To The Test For Free! Let Us Give You a Solution.