DC Truck Vibrators Help Manlius Township
Published: January 5th 2016
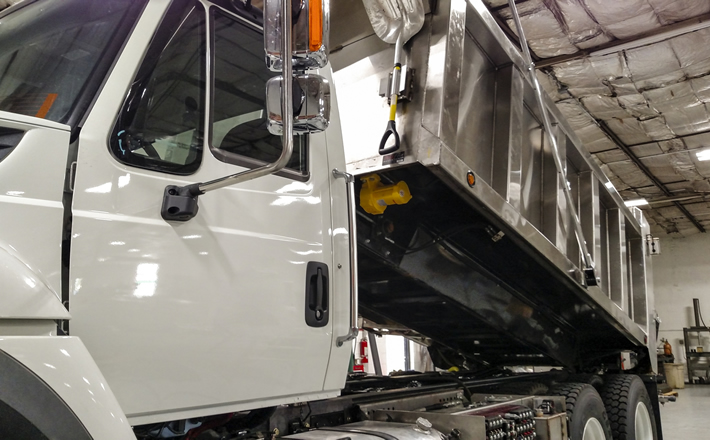
[Neponset, IL] – A township in Illinois has drastically improved production and increased worker safety by installing heavy duty truck vibrators to completely empty adhered material from its dump trucks without worker intervention. Manlius Township was having problems with gravel, rock salt and dirt sticking to the bed of its plow-equipped dump trucks, causing drivers to get out and shovel or use dislodging methods that could harm equipment. To avoid potential hazards, officials installed a Cougar® DC-3200 12V Truck Vibrator manufactured by Martin Engineering. After one year of use, truck operators report that the reduction in offloading times due to more rapid and complete evacuation of material has added 4 to 5 cargo runs per day and more control over cargo distribution, resulting in less strain on equipment and improved safety of workers.
The heavy-duty dump trucks are equipped with plow attachments and 7-yard boxes, controlled by a hydraulic lift. They are dispatched to various jobs throughout the township, located southwest of Chicago. “We use our dump trucks for all kinds of jobs, from public works projects to winter road maintenance,” said Road Commissioner Rob Allen. “Each project has its unique problems, but one issue we had across all of them was material sticking to the truck beds.”
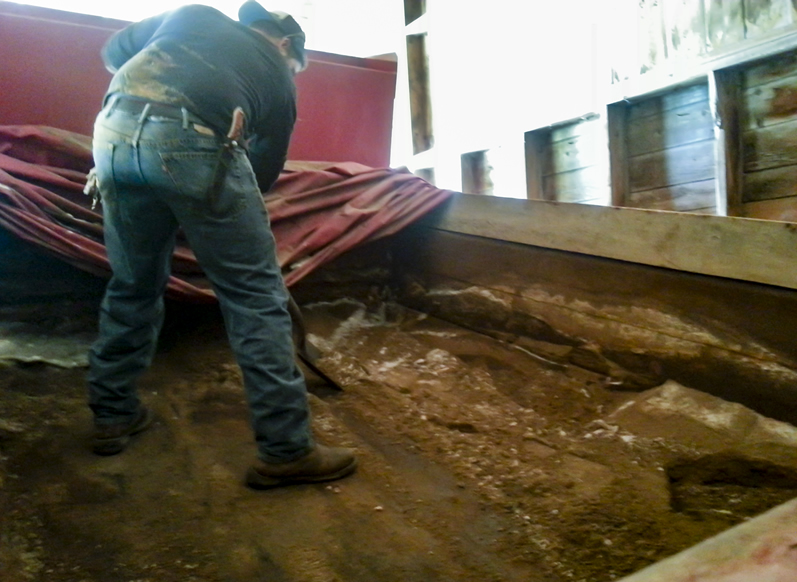
Dislodging
Before Manlius installed truck vibrators, drivers used various methods to evacuate material from the bed. One technique involved controlling the hydraulic lift from inside the cab, causing the box to move up and down abruptly to shake material loose. This can cause expensive wear and tear on the vehicle and the hydraulic system and was not effective. Another method involved lifting the box to the highest angle, driving the vehicle forward, and stopping suddenly, causing the recoil to dislodge material. Although no accidents occurred as a result, the action could create a top-heavy vehicle to tip over. In addition, it puts tremendous strain on the hydraulic lift, engine and brake system.
The most effective method of evacuation involved drivers setting the cargo box at a slight incline, climbing into the bed and shoveling cargo out manually. This task presented a host of potential risks, including slip and falls, unexpected loosening of debris underfoot – resulting in sudden offloading – and exposing workers to extreme weather. Beyond the potential liability and injury issues, the task was very time consuming and labor-intensive, taking between 30 and 60 minutes per load.
Testing Vibration
Managers were skeptical about implementing vibration at first and requested a field test of the Cougar side-by-side with a competitor. “They had purchased several units from another company in the past, with only moderate results,” said Allen Twidell, Mobile Markets Manager for Martin Engineering. “Though more debris was loosened than before, drivers still needed to shovel after every load, which defeated the purpose.”
Specially designed for heavy-duty applications, the small and lightweight units from Martin Engineering require minimal space. A single Cougar® DC-3200 12V Truck Vibrator was installed at the top center underneath the truck’s cargo box, near the cab, and was connected to the truck’s electrical system. Activated from inside the cab, the units are available in 12-24 volt high-speed, low amp motors. “The weatherproof aluminum housing provides a high output-to-weight ratio and is tightly sealed to protect the internal components and permanently lubricated ball bearings from dust and abrasion,” Twidell added. Delivering up to 3200 pounds of force, the small but powerful vibrator improves the unloading of wet, sticky, fibrous or frozen material.
For the field test, the Cougar® DC-3200 12V Truck Vibrator and the competing vibrator were connected to different trucks and used for a few days, then the drivers were consulted on each unit’s performance. They reported that the competitor’s vibrator left cargo stuck to the corners and bed of the box, requiring the driver to shovel out the remaining material, whereas the Cougar® DC-3200 12V Truck Vibrator emptied its load quickly and completely. “I’ve been around dump trucks with vibrators most of my life, and I’ve never seen anything shake like that,” said Allen.
Controlled Offloading
Even and measured distribution of cargo helps improve the quality of winter road maintenance and public works projects. During snowy Illinois winters, spreading the full load of salt evenly across the road helps avoid dangerous ice patches and improves the safety of drivers. Full evacuation of cargo maximizes the amount of road each truck can cover per run, increasing efficiency.
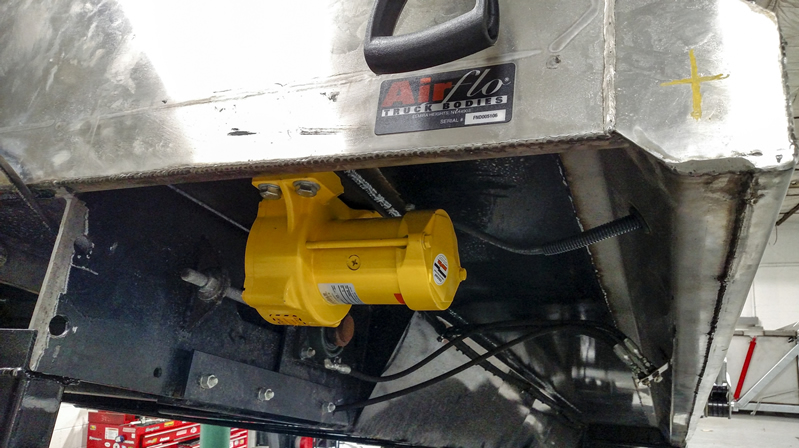
When applied to the construction of gravel surfaces, organized distribution of material is also important. "The vibrator preps the road surface by spreading gravel evenly from the truck bed, saving grader time," said Allen. “It’s almost like spreading it with a knife.”
Prior to vibration, operators laid down the gravel, then passed over it as many as half a dozen times with a road grader to achieve a flat surface. Even after grading, gravel roads still experienced a washboard effect, with small “waves” of material that produced chatter bumps. Using vibration with the proper offloading angle, operators found that it took just one pass with the grader to smooth the surface, improving the long-term quality of the road and decreasing chatter from driving on it.
Results
After one year of use, managers report that the Cougar® DC-3200 12V Truck Vibrator have significantly increased the amount of material hauled per day. Time spent plowing and salting roads is more productive, with less downtime trying to clear uncooperative loads. Road grading and hauling from public works projects have also experienced increased productivity. The township expects longer equipment life, greater efficiency and increased safety for employees and motorists.
“We’re impressed with the performance,” said Allen. “I would recommend this unit to anyone who owns a dump truck.”