Martin® Hurricane Air Cannons Help Martin Marietta
Published: January 18th 2016
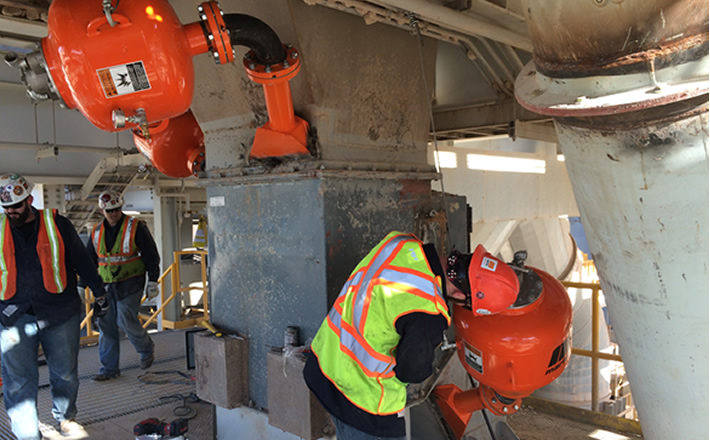
[New Braunfels, Texas] – A global innovator of bulk material handling technologies has used high-performance air cannons to help a cement plant prevent material backup due to a clogging transfer chute. With a total production of 2.3 million tons annually, the Hunter Cement Plant in New Braunfels, Texas – owned and operated by Martin Marietta – experiences heavy rain dousing raw material on its partially covered, tower-mounted D-07 conveyor system. Wet dust and aggregate would clog the chute and cause backups on the belt, leading to spillage issues that halted production and took 6-8 hours to clear. The solution employs a series of Martin® Hurricane Air Cannons strategically placed along the chute to improve material flow, minimize unscheduled downtime and reduce clean-up.
Limestone extracted from the Hunter quarry is crushed to a size of 6-inch minus (150mm) and mixed with clay, then conveyed to a processing tower. Separate conveyors deliver iron ore and sand to the same tower and the two chutes offload 350 to 400 tons (317.5 to 362.8 metric tons) per hour onto the D-07 conveyor, mixing them together on the 42 in. (1068 mm) single belt running at 350 FPM (1.8 MPS).
The conveyor travels approximately 300 feet (91.4 m) to an adjacent tower and offloads into a pyramid-shaped funnel, which feeds a chute 12 foot-long (3.65 m), 3 ft. by 3 ft. (.91 m) square chute with a flow control gate at the bottom. The gate either diverts material to a conveyor leading to the raw mill or to a dump truck waiting on the ground below. Operators found that wet or damp material gradually formed into a rat hole and eventually created an obstruction, which led to the material back-up.
When the material flow began to choke off, two or three workers would gather around the railing at the top of the chute and use air lances and pneumatic jackhammers fitted with 8-foot long bits to clear the obstruction.
According to a management source, “The frequent unscheduled downtime to clear the rotary feeder chute was a challenge. We approached Martin Engineering to explore the possibility of adding air cannons that could help resolve the bottleneck issue.”
Air Cannon Placement for Proper Flow
Martin technicians installed a total of five Martin® 70-L Hurricane Air Cannons on two levels. The 94 lb. (43 kg) tanks are suspended from the tower frame by steel cords and are fed by the plant’s existing compressed air system. They fire a shot of air at up to 120 PSI (8.27 BAR) from a pressurized tank through a fan jet nozzle with a 12-inch (305 mm) wide mouth, which spreads the stream across the surface area of the wall. To clear obstructions and assure proper material flow, the cannon has an effective area of up to 22.6 ft3 (640 L).
On the upper level, two of the cannons were placed along either side of the chute to dislodge accumulation from the wall, and a third unit was installed at the top to free any material that could get trapped where the chute narrows. One floor below, a cannon is directed at a downward angle to aid material flow, whereas the lowest unit on the chute specifically addresses the easily clogged diverter gate.
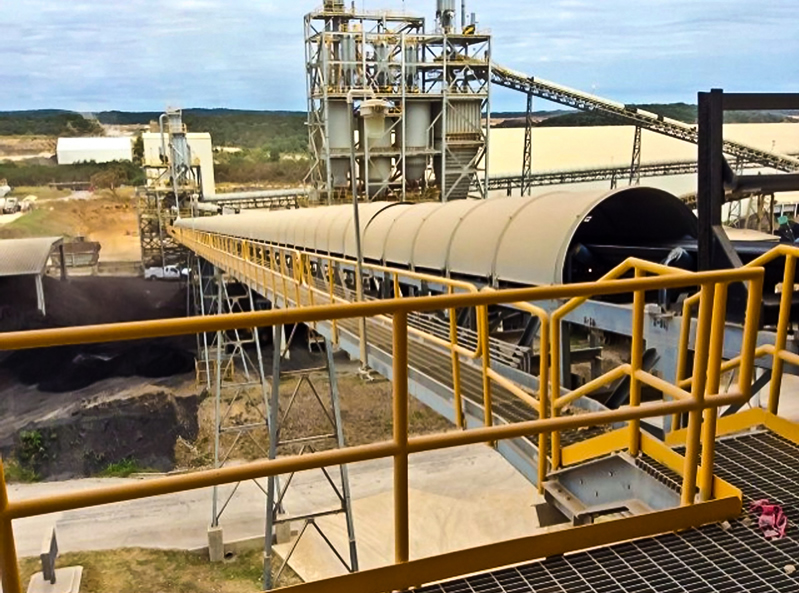
All fitted with a centrally located valve design, the tanks offer a direct air path with maximum force output and low air consumption. This efficiency reduces the burden on the compressor and shortens the lag time between sequences. The central valve is a detachable component that allows a single worker to disconnect it without the need to remove the tank, for faster and easier maintenance.
A 10-bank positive solenoid control panel is connected to the facility’s programmable logic control (PLC) software, allowing operators to control and monitor the proper firing time and sequence from a remote location. To eliminate the risk of unintentional firing due to drops in pressure, the valve requires a positive signal from the solenoid in the form of an air pulse to trigger discharge.
Result
A few months after the installation, operators report that the air cannon solution has significantly decreased the plugging issues, resulting in continuous operation with minimal unscheduled downtime. Moreover, the area around the chute is reported to need only routine cleanup and maintenance accompanying normal scheduled inspections.
“Due to our long and positive relationship, we were confident that the Martin Engineering team was going to come through,” Martin Marietta management concluded. “The equipment has worked out well, and with the team’s consistently attentive service, we are confident that this is a good solution.”
Along with hundreds of air cannons, Martin Engineering has also equipped the Hunter Cement plant with conveyor accessories and bulk handling solutions.