Published: August 2nd 2016
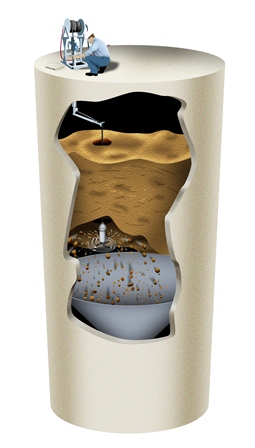
Eagle Materials is a leading U.S. manufacturer and distributor of building materials, including Portland cement, concrete, gypsum wallboard and aggregates. Founded in 1964, the company is one of the nation’s largest cement providers, with four plants supplying a combined total of about 4 million tons annually. The company’s Illinois Cement facility in LaSalle manufactures approximately 1.1 million tons of that total each year.
Like most cement manufacturers, the plant uses large storage vessels to hold finished material until it’s ready for shipment. At the LaSalle facility, the domed storage unit is 99 feet tall and 186 feet in diameter, capable of holding about 80,000 tons of Type I cement. A reclaim screw conveyor (auger) is used to deliver material to a belt conveyor for load-out from a tunnel beneath the dome. This reclaim conveyor is supported by a cable that allows operators to raise and lower as needed.
During the course of normal operations, the cable connectors worked themselves loose, causing the auger to fall onto the pile and halting the flow of material. The only way to rectify the situation was to position a crane over the reclaim screw and lift the conveyor out so the cable could be reattached. But to do that, operators first needed to clear out enough material to access the disabled equipment, a massive task in light of the nearly-full dome.
“Our first step was coming up with a plan to tackle the load-out job,” recalled Chief Chemist and Quality Control Manager Kevin Jensen. “We needed to remove a significant amount of material in order to make the repair, and there was just no easy way to go about it.”
Jensen contacted Martin Engineering (Neponset, IL) for assistance, and technicians were on site to inspect the situation the next day. The two companies reviewed the options, and it was determined that the best approach was to employ the Martin® Heavy Duty Whip, one of several technologies that make up the company’s Silo Solutions product line.
The Whip is a portable, remote controlled tool that can be lowered into storage containers through a manhole opening. Powered by compressed air, the patented gyro motor uses a variety of flails and cutting edges to knock down accumulated material without damaging storage vessels. Abrasion-resistant steel chain is best suited for most applications, with non-sparking brass chain for combustible materials. Urethane flails can also be employed to protect lined vessels that could be susceptible to damage from metal tools.
“With this technology, there’s no need to send a man inside a bin and risk injury,” observed Martin Engineering Territory Manager Jim Densberger. “The equipment can be set up quickly outside the vessel, and it’s portable enough to move easily around various bin sizes and shapes.” In most cases, the technique allows material to be recaptured and returned to the material stream.
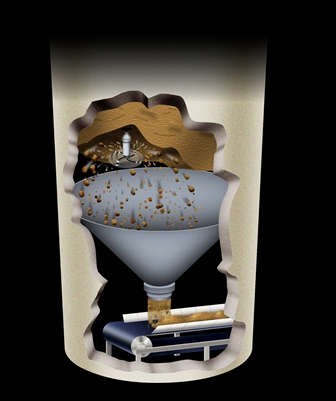
With safety harnesses in place, Martin Engineering technicians secured the equipment through an access hatch at the top of the dome. Though all of the company’s silo cleaning crews are OSHA and MSHA certified for confined space entry, they instead used remote control from outside the vessel to safely guide the head. The 2-man crew lowered the whip through an opening in the blockage, then worked their way downward from above, dislodging material as they went. By undercutting the wall accumulation, it eventually began falling in sections from its own weight.
The modular boom of the Martin Heavy Duty Whip extends up to 8.5 meters (28 feet) and can clean vessels up to 18 meters (60 feet) in diameter from a single central opening of just 450 mm (18 inches). Air hose is protected with double wire braid, and the pneumatic motor delivers powerful whip action from the rotating head to remove buildup from walls. The hose reel easily separates from the boom assembly for transportation and set-up in tight spaces.
“There are competing systems that run on hydraulics, but they tend to be heavy and cumbersome to move,” Densberger continued. “And they present the possibility of a fluid leak, which could damage otherwise-salvageable material. The whip requires no hydraulics; it needs just 90 PSI and 100 CFM, which can usually be supplied from a plant’s existing air system.”
Densberger added that some pneumatic cleaning systems require very high air volumes, often as much as 1,200 CFM. “To achieve that kind of pressure, the diesel compressor rental alone can be more than $1,000 a day, and the fuel bill for a full day’s work could be half again as much,” he said. “Then there’s the cost to actually do the work.”
Potential damage to the storage vessel can also be an issue. Some cleaning technologies use the very high pressure to blow air through a hose that’s simply dropped into a 6" access hole at the top of the vessel. At the end of the hose is a cutting tool with a restricted nozzle of just 1/2" or so, which causes the cleaning head to thrash about randomly. While this technique works well in large blockages, as the head gets closer to the vessel wall, it has roughly as much chance of taking out a chunk of the silo as it does hitting material for removal.
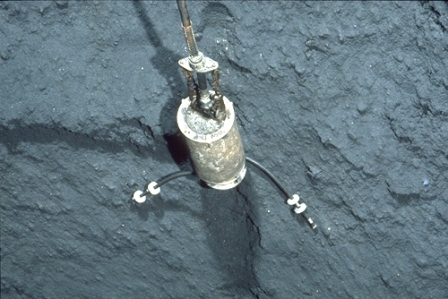
The Martin Engineering crew operated around the clock on the Illinois Cement project. Technicians were on-site for nearly a month. “During the process, we were able to use our auto load-out system from the bottom of the dome, because the material being knocked down fell primarily in the center,” Jensen observed. “There was no need to transfer cement in the tunnel, and that helped minimize the disruption.”
With the reclaim conveyor repaired and the process back up and running, Jensen was asked to summarize the experience. “The crew’s performance was excellent,” he concluded. “Martin Engineering was very responsive, and provided an innovative solution to the problem. We had good communication throughout, and all work was done in a safe manner.”
Eagle Materials has been manufacturing cement in the U.S. for more than 40 years, with plants strategically located in Illinois, Nevada, Texas and Wyoming. In 2007, the Illinois Cement facility completed a significant upgrade and expansion, facilitating a dramatic improvement in manufacturing capacity, energy consumption and per-unit production costs. Capacity increased to 1.1 million tons, while the cost structure was reduced by 20%.